The "MEGAMACS"
mobile tank cleaning device
The "MEGAMACS"
mobile tank cleaning device
MegaMACS is an in situ solution, allowing for the processes of tank cleaning and waste processing to be done by one machine.
The MegaMacs system is a mobile, energy independent solution that is easily adaptable for local conditions and variety of projects related to cleaning tanks, pits, etc. The system is modular and can meet any customer's requirements.
The main unit extracts sludge, performs preliminary sludge separation and is able to clean tanks to the level of welding repairs. Production capacity is up to 15 cubic meters/hr of sludge.
The three-phase centrifuge further separates removed sludge (a mix of oil, water, solids) received after main unit processing. The output content depends on the initial sludge composition and customer requirements. Excellent oil quality can be achieved using this unit. Production capacity is 15 cubic meters/hr.
Both units are completely mobile and energy independent. They are moved around by a regular truck with 5th wheel device. As the units finish cleaning one oil storage tank, they are trucked to the next tank. The time required for mobilization and demobilization is 4 hours each. The units able to operate up to 150 m. from the tank and can be placed outside the bund-wall.
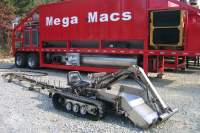
CUTTING-EDGE, MOBILE SLUDGE REMOVAL AND PROCESSING SYSTEM
EFFECTIVE SOLUTIONS, SUPERIOR RESULTS
The MegaMacs system can, on average, clean a 10,000 cubic meter tank in less than a week.
MegaMacs have been used for tanks from 5,000 to 120,000 cubic meters. The oldest system has been in operation for 16 years. The best available off shelf components are used in the system construction, making it easy to maintain with readily available spare parts.
Equipment pay off time depends on local regulations and conditions. The average pay off time for a MegaMacs system is 13 months.
MegaMacs have been used for tanks from 5,000 to 120,000 cubic meters. The oldest system has been in operation for 16 years. The best available off shelf components are used in the system construction, making it easy to maintain with readily available spare parts.
Equipment pay off time depends on local regulations and conditions. The average pay off time for a MegaMacs system is 13 months.

DISCOVER THE BENEFITS
There are countless benefits to employing the MegaMacs system:
- Safety of operations
- Reduced cost of cleaning per cubic meter
- Improved tank turn-over through faster cleaning
- Reduction of environmental impact
- Reduction of disposable toxic disposal (up to 10 times)
- Oil recovery as a sellable byproduct
- No electrical devices to improve safety
- Improved working conditions
- Better cleaning quality
- Practically no preparation and construction cost
- Utilities on site are not required
- No lifting equipment required for equipment mobilization/de-mobilization
- No tank alterations

COMPREHENSIVE SOLUTIONS
There are countless benefits to employing the MegaMacs system:
Our MegaMacs system has been successfully used to clean sludge from crude oil storage tanks of transnational upstream and downstream companies all over the globe (Europe, Asia, Africa, South and North America).
We offer turnkey solutions to our customers including:
- Technology design, manufacturing and equipment delivery
- System startup, commissioning and personnel training
- Warranty and after warranty technical support and service

DISCOVER THE MANY ADVANTAGES OF MEGAMACS
Modular construction means faster on-site set up. MegaMacs has a power source to drive various equipment used to remove sludge from the vessel being cleaned. Each of the main modules are installed on standard wheeled chassis with a saddle for common truck connection, as well as lighting and brakes to make them fully portable and to eliminate the need for cranes or heavy lifting devices during job site set up. No on-site preparation is required. Both modules are equipped with hydraulically operated legs, which allow for levelling and use on uneven surfaces.
All MegaMacs equipment is hydraulically driven. The system continuously monitors the atmosphere inside the tank and common grounding. Should one of the parameters be out of balance, the system has a built in automatic shut down. The system requires limited personnel presence inside the tank.
The MegaMacs system is innovative, ergonomical, and extremely operator friendly. The system is designed for automated tank cleaning - minimum manual work is involved during cleaning process. The MegaMacs system is highly flexible. Initially it was specifically designed for crude oil storage tank cleaning, but its evolution has allowed it to be used for variety of different applications such as oil sludge pits and lagoon cleaning, catalysts storage tank cleaning, rail road tanker cleaning, as well as the cleaning of various vessels, barges, etc.
Use of the MegaMacs system will reduce disposable material up to 10 times. Previously disposed hydrocarbons are returned to the customer, and there is a drastically reduced impact of contaminated materials transportation. The site is never contaminated, preserving it in original conditions.
The system consumes minimal water or cleaning solution during washing operations through the use of water or cleaning solution re-circulation. A fully automated system, there is minimal operator exposure to risk inherent environments.
The system consumes minimal water or cleaning solution during washing operations through the use of water or cleaning solution re-circulation. A fully automated system, there is minimal operator exposure to risk inherent environments.
MegaMacs is able to clean large storage tanks (from 5000 to 200000 cubic meters) containing commodities such as crude oil, bunker fuel, slop oil, asphalt, etc. The system can also be employed for cleaning railcars and auto tankers, and pipelines. Ideal for processing of drummed sludge and cleaning the drums, cleaning and processing of API ponds and environmental cleanup such as an oil spill from LCC (Large Crude Carrier). The MegaMacs system can handle any processes from heavy sludge to light oils.
Personalized factory support and training insures years of worry-free operation.
Modular
construction
Safety
throughout
cleaning
Maximum
process
mechanization
and system
flexibility
Environmentally
friendly
Unparalleled
efficiency
Top notch
factory support
TAKE A LOOK AT THE MEGAMACS SYSTEM
